CONSTRUCTION


CONSTRUCTION MANAGEMENT
RII believes in providing a consistent project delivery experience. Early on in a young Project Manager’s career, we pair an individual with a mentor that allows him/her to experience the realities of what it takes to make a project successful. This mentorship affords the individual an opportunity to gain the necessary hands-on experience to manage a project on his/her own.
RII knows the key to successful project management lies in clear communication and documentation as well as a seamless transition from drawing the project on paper to erecting it in the field. Using BIM and BUILDERTREND, allows all our project managers, superintendents, project engineers to access real time information and constant communication.
SAFETY
We strive to create a safe work environment by encouraging employees to be proactive, not reactive, on all safety issues. At RII, we take great pride in the premier group of people who make up our team. From our Ironworkers and Glaziers in the field to our Shop, Yard and Office Staff who support their efforts, our focus is on performing each and every job safely.​
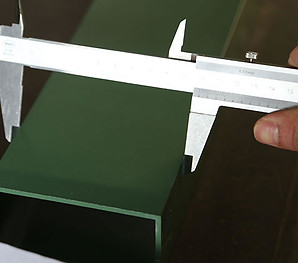
QUALITY
The quality process begins with a comprehensive understanding of the Owner’s expectations and a project centric approach. Throughout the preconstruction process we work with the Project Team to develop complete contract documents and details that communicate the design intent and performance expectations to our Project Staff, supply chain partners, and installation crews in the field, thereby setting minimum standards for quality.
​
Mockups, including first run studies and early completion of standard units, are commonly used to establish quality benchmarks and expectations to demonstrate required levels of quality. Mockups also become tools for crew education and allow the field to self-evaluate performance both in the initial stages and continuing throughout the project. With each mockup, we identify different means and methods to increase our efficiency in the field, identify areas that need the critical attention of our field crew, certify the thermal performance, and identify any water infiltration issues before the first panel is ever installed on the building. They provide the owner assurance that their building will stand the test of time and perform as expected.
​
Through the application of Lean Principles, quality expectations in the form of task-based quality checklists are used to create predictable work flow and promote rapid learning. With the integration of quality review into the construction process, we also create seamless transitions as the work is passed to new crews, or as multiple crews are added as needed to meet the schedule.